Kearney, MO Residential HVAC & Plumbing Services
LBA Services was started by people just like you who want and insist on high quality and reliable service. In Kearney, MO and throughout the Kansas City area, we treat each family and home as if it were our own. That includes rising to the challenge of being a Hero any time the need calls for extraordinary measures.
From routine maintenance to 24/7 emergency repairs, LBA Services has you covered for all your home plumbing, heating, and air conditioning needs. The same goes for new and replacement system installations. Read our reviews and find out why your neighbors consider us to be their nearby heating and air company and local plumber in Kearney, MO.
Recent Jobs and Reviews in Kearney, MO
Customers say: The provided content describes the overall sentiment of the reviews as positive. The reviews mention specific individuals who were helpful, professional, informative, trustworthy, patient, thorough, friendly, knowledgeable, and helpful. There are also mentions of quick and efficient service, confidence in choices, and satisfaction with the work performed. However, there are also negative reviews that mention issues with pricing, communication, and the experience with technicians. Overall, the sentiment is positive, with more positive reviews than negative ones.
Our Local Reviews by City
- Adrian, MO (2)
- Avondale, MO (1)
- Basehor, KS (21)
- Bates City, MO (1)
- Belton, MO (31)
- Blue Springs, MO (56)
- Bonner Springs, KS (30)
- Buckner, MO (1)
- Bucyrus, KS (6)
- Columbia, MO (1)
- De Soto, KS (22)
- Dearborn, MO (1)
- Edwardsville, KS (14)
- Eudora, KS (9)
- Fairway, KS (88)
- Freeman, MO (1)
- Gardner, KS (14)
- Gladstone, MO (63)
- Grain Valley, MO (32)
- Grandview, MO (69)
- Greenwood, MO (1)
- Houston Lake, MO (7)
- Independence, MO (175)
- Kansas City, KS (397)
- Kansas City, MO (2744)
- Kearney, MO (3)
- Lake Lotawana, MO (4)
- Lake Quivira, KS (18)
- Lake Waukomis, MO (4)
- Lansing, KS (2)
- Lawrence, KS (19)
- Leavenworth, KS (7)
- Leawood, KS (408)
- Lee's Summit, MO (150)
- Lenexa, KS (577)
- Liberty, MO (104)
- Lone Jack, MO (1)
- Louisburg, KS (5)
- Merriam, KS (20)
- Mission, KS (195)
- Mission Hills, KS (74)
- North Kansas City, MO (10)
- Northmoor, MO (1)
- Oak Grove, MO (9)
- Odessa, MO (1)
- Olathe, KS (591)
- Ottawa, KS (1)
- Overland Park, KS (1369)
- Parkville, MO (182)
- Peculiar, MO (1)
- Platte City, MO (12)
- Pleasant Hill, MO (1)
- Pleasant Valley, MO (3)
- Prairie Village, KS (506)
- Prairie Village New, KS (2)
- Raymore, MO (24)
- Raytown, MO (74)
- Riverside, MO (15)
- Roeland Park, KS (181)
- Shawnee, KS (990)
- Shawnee Mission, KS (1)
- Smithville, MO (1)
- Spring Hill, KS (11)
- Stilwell, KS (61)
- Sugar Creek, MO (7)
- Weatherby Lake, MO (26)
- Wellsville, KS (1)
- Westwood, KS (27)
- Westwood Hills, KS (17)
Job Locations and Reviews

Clean and seal
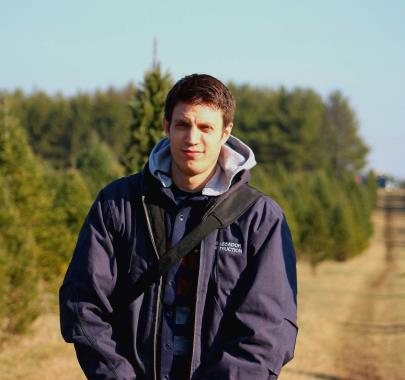
Called jim
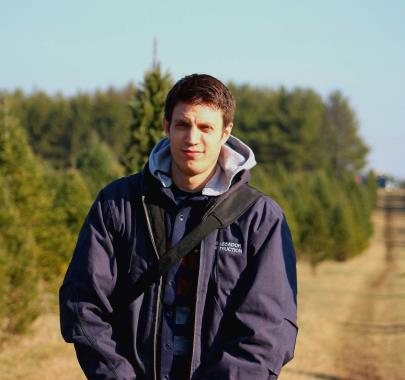
Aeroseal
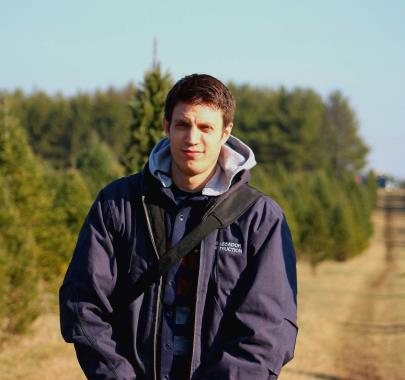
Completed Spring maintenance. Renewed Club Membership and installed SmartAC Sensors.

Completed furnace maintenance and inspection. I checked all components and amp draws. Cleaned up furnace and flame sensor. I found no issues with furnace at this time other than dust getting inside system. Ran heat pump and found common wire to capacitor burnt. Contactor had rust building up as well. Found out that there’s a sprinkler system causing this. With customer permission I replaced Contactor, fixed burnt wire, added hard start kit and added foam tap to help keep the water out. All operations were within manufacture specs at departure.

Dropped off electrostatic media filters that I did not have in stock in my van at the time of AC maintenance.

Arrived at the customers home to perform an AC maintenance. Upon arrival I put the system into cooling mode and began by checking static pressure. Static pressure passed at this time. I performed a CFM count which was also passing. I checked all electrical levels which were within manufacture specifications today. I inspected the blower wheel assembly for cleanliness and excessive play in the shaft. The blower wheel assembly looked good today. I performed a temperature split between the supply and return air which was 20 degrees. I moved to the outdoor unit and checked all electrical and refrigerant levels. Refrigerant levels were good today but I found the compressor to be drawing over the allowed amps on start up. I spoke with Jim about my findings and proposed installing a hard start kit to help the compressor on startup. I also recommended doing an extensive coil cleaning today. Jim decided he did not want to go with the options today. I washed the outdoor coil with water, and the

Upon arrival I began the AC tune up. I found the static pressure was failing at .7 when it is rated for a max of .5 but the manufacturer wants it at 80% of the max which would be .4. I checked the cooling Delta T level which was good at 18 degrees. The blower wheel is caking up with dirt. The running amps on the blower motor are a little high at 9 running amps. The capacitor on the blower was at 100%. The dual run capacitor on the outdoor condenser unit was at 100% as well. Customer asked me not to check the refrigerant levels. The running amps on the fan and compressor were within limits. Customer opted not to have a field supervisor out to find a solution to the static failure issue.

Double return,12x24 secondary boot, and EAC filter
Always courteous, reliable technicians, great communication from the company letting you know when they will arrive etc.
First checkup on 1 year old systems. This guy took the time to be sure everything was right. LBA has impressed me from day 1.
Knowledgeable, friendly, professional