Kansas City, KS Residential HVAC & Plumbing Services
LBA Services was started by people just like you who want and insist on high quality and reliable service. In Kansas City, KS and throughout the Kansas City area, we treat each family and home as if it were our own. That includes rising to the challenge of being a Hero any time the need calls for extraordinary measures.
From routine maintenance to 24/7 emergency repairs, LBA Services has you covered for all your home plumbing, heating, and air conditioning needs. The same goes for new and replacement system installations. Read our reviews and find out why your neighbors consider us to be their nearby heating and air company and local plumber in Kansas City, KS.
Recent Jobs and Reviews in Kansas City, KS
Our Local Reviews by City
- Adrian, MO (2)
- Avondale, MO (1)
- Basehor, KS (21)
- Bates City, MO (1)
- Belton, MO (31)
- Blue Springs, MO (56)
- Bonner Springs, KS (30)
- Buckner, MO (1)
- Bucyrus, KS (6)
- Columbia, MO (1)
- De Soto, KS (22)
- Dearborn, MO (1)
- Edwardsville, KS (14)
- Eudora, KS (9)
- Fairway, KS (88)
- Freeman, MO (1)
- Gardner, KS (14)
- Gladstone, MO (63)
- Grain Valley, MO (32)
- Grandview, MO (69)
- Greenwood, MO (1)
- Houston Lake, MO (7)
- Independence, MO (175)
- Kansas City, KS (397)
- Kansas City, MO (2744)
- Kearney, MO (3)
- Lake Lotawana, MO (4)
- Lake Quivira, KS (18)
- Lake Waukomis, MO (4)
- Lansing, KS (2)
- Lawrence, KS (19)
- Leavenworth, KS (7)
- Leawood, KS (408)
- Lee's Summit, MO (150)
- Lenexa, KS (577)
- Liberty, MO (104)
- Lone Jack, MO (1)
- Louisburg, KS (5)
- Merriam, KS (20)
- Mission, KS (195)
- Mission Hills, KS (74)
- North Kansas City, MO (10)
- Northmoor, MO (1)
- Oak Grove, MO (9)
- Odessa, MO (1)
- Olathe, KS (591)
- Ottawa, KS (1)
- Overland Park, KS (1369)
- Parkville, MO (182)
- Peculiar, MO (1)
- Platte City, MO (12)
- Pleasant Hill, MO (1)
- Pleasant Valley, MO (3)
- Prairie Village, KS (506)
- Prairie Village New, KS (2)
- Raymore, MO (24)
- Raytown, MO (74)
- Riverside, MO (15)
- Roeland Park, KS (181)
- Shawnee, KS (990)
- Shawnee Mission, KS (1)
- Smithville, MO (1)
- Spring Hill, KS (11)
- Stilwell, KS (61)
- Sugar Creek, MO (7)
- Weatherby Lake, MO (26)
- Wellsville, KS (1)
- Westwood, KS (27)
- Westwood Hills, KS (17)
Job Locations and Reviews

Replaced furnace with proper size

AC Repair Service: The client’s AC system was experiencing short cycling. I diagnosed low refrigerant as the issue and restored levels to the manufacturer’s specs. This improved cooling performance and prevented system strain.

I performed a light maintenance. replaced all filters and tested each system cooling functions. Everything had great temperature splits and running as they should be at this time.
Andrew did a great job. He conducted his examination of our heating and cooling system thoroughly and explained his findings clearly. He is a true professional.

Estimate

B
Perfect
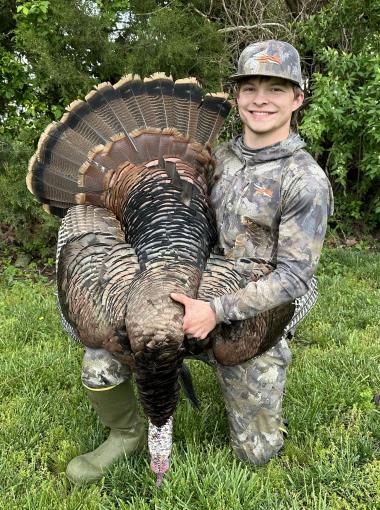
Furnace is up and running safely. The rollout switch went off. I reset it and tested for carbon monoxide. There is no carbon monoxide present. Thank you for choosing LBA services!

Springtime AC Tune-Up: To prepare a home for the summer, I cleaned evaporator coils, checked refrigerant levels, cleared condensate drains, and optimized airflow, ensuring peak performance.

AC Unit Repair: A homeowner reported weak airflow from their AC unit. Upon inspection, I discovered a misaligned blower fan, which I promptly realigned, restoring optimal cooling performance.

Arrived for ac maintenance today. Checked static pressure and it is failing at this time. Blower wheel is clean. All electrical components are running properly at furnace. There’s a good temperature split between the return air and supply air. At condenser pressures and charge look good. Capacitor is still testing good. All electrical components are running properly. I rinsed coil clean. System is running upon departure. Thanks for choosing LBA.

Clean

Today there were two furnaces, two condenser (on roof), one rtu and one hot water heater that were both mechanically and electrically inspected. The hvac units were operated and checked in both heating and cooling modes. The hot water heater was checked for leaks, proper drafting, temp cycling and was set back to low temp. The rooftop unit did have several deficiencies that is preventing it from functioning properly. All findings were relayed to Blake and he will contact us for further assistance if needed. A check sheet was completed and emailed to him as well. Due to the issues with the rooftop unit some extra time was spent diagnosing the issue with the heat mode. Thank you. Jon

New Halo and new humidifier

Upon arrival the homeowner explained there was a yellow or orange error type message on his thermostat a couple of days ago. He pressed on that button and it went away. I pulled up the alerts on the thermostat but none were listed. I advised that if it happens again to try taking a picture of the thermostat so that we can see what code or alert it is trying to send. I checked the system in heating and in cooling modes today. Both are working properly at this time. Ray came outside to the AC with me and noticed how quiet the new AC runs. It’s impressive how quiet they are able to manufacture new systems these days. If you have any trouble with anything on your system please don’t hesitate to give us a call. Your LBA Technician, Tyler Rickard P.S. No payment was due for todays visit, it was covered with your membership. Have a great rest of your week!

Halo 5 and humidifier install sold for tomorrow

Called
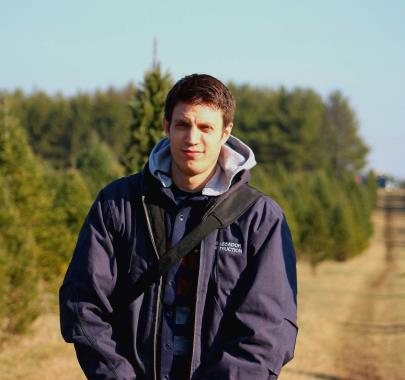
After checking the AC and electric furnace everything is operating well. All safety switches and electronic components in the air conditioner heat pump and electric furnace are operating well within manufactured specifications. Refrigerant levels are good and air temperature coming out of vents as well as the Delta temperature is good. when I was checking the humidifier. I noticed no water was coming out And then check voltage to make sure that the humidistat was working properly. After I checked the saddle valve that is connected to the water heater. It was clear that we had issues with hard water calcifying the connection. Because of this no water was coming out of the saddle valve. I then tested the solenoid valve to see if that was operating, and it was also clogged with calcium. Because these two separate parts cost more to purchase and install than a humidifier itself replacing the humidifier is the obvious choice. However, if we put in a new humidifier, we will still have issues

Installed new frost-proof hose bib hydrant. Thanks for choosing LBA Services! Your technician Jeremy
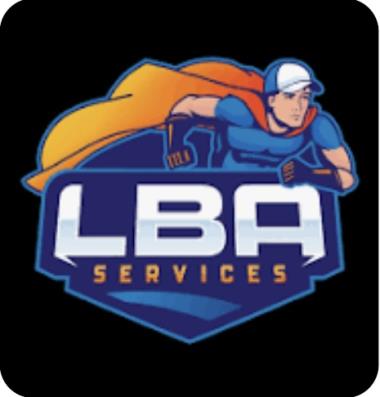
Sold outdoor hose spigot repair. Proposed water heater w/txt and stops as well but just the repair for now.

Inspected outdoor faucet, looked over plumbing, turned over to supervisor

No answer on phone call, left voicemail

3/28/25 Due to equipment outages the lift is not available. Spoke with Dane and the decision to postpone today’s repair to early next week was made. 2hrs labor ()()()()()((((()((()()*()*)&($($)$(#(#(

Customer wasn’t home to finish up financing paperwork.

Hot water stop shutoff was in the off position. Hot water is now flowing! Thanks for choosing LBA Services! Your technician Jeremy

Left a voicemail to work with the customer on Financing approval

I installed a PRV (pressure regulating valve) and set to 65 lbs/in, re-piped some copper with PEX piping above washer machine on hot water line through the floor into kitchen, installed a new water stop shutoff on hot line underneath kitchen sink, installed a new pvc p-trap drain underneath lower lever bathroom sink, installed new water stop shutoff on hot water line underneath upper level bathroom sink, and installed new 2 handle tub/shower valve and new trim kit w/ new shower head. Thank you for choosing LBA Services! Your technician Jeremy
Professional service
The tech is like family. He takes the time to explain things. They are not trying to "up sale" unnecessary items. He takes the time to make recommendations in a timely fashion.
The guys did good
The guys did good
John is the best! He kept us informed each step of the way. Very professional.
Excellence service
Very knowledgeable, pleasant, went right to work. I had a great experience.
Showed up on Super Bowl Sunday and at least got us running while my unit thawed out
I was thankful they were able to get a plumber out to my house quickly for a sink leak, but that was the only benefit. After booking a 5 hour show up window, i was then called that they were on their way 1.5 hours before my time (which, if i wasn’t at work, may have been nice, but i had to take off work to allot for this time frame). Then, after they arrived, i didn’t realize they wouldn’t be doing the work right then, that they were just assessing and getting a quote. I wish that it had been communicated that the visit was just a consultation. I do like their texting capabilities. But i was frustrated with my recent visit.
They’re very easy to work with and technicians are friendly courteous and knowledgeable.
Very thorough and informative . Very polite and respectful.
Very thorough and imfomotive. Very polite and respectful.
Very nice and knowledgeable!
As far as Nick goes he is the one that showed up and i am pleased with everything how he explained to me the problem witht the unit. Keep Him
The major problem is i had several text saying someone was going to go fix it i thinking like 3 or 4 names was on my text that was on thier was to my locatin and no one ever showed up when the text said they be there then duriing the 3 day waiting i finally had the tech show up and did the reapai.
Andrew did a great job checking my furnace and explaining things.
Very good service
Work was completed efficiently and expertly. And they cleaned up everything
Excellent service!
Cornelius took his time to explain thoroughly why he was there and what would be taking place. He was professional, knowledgeable, thorough, and kind. He took special care to explain my options and made sure I was aware of the results of my inspection.
Great service
Technician was very courteous and knowledgeable.
Thank you for such good service
Both guys did a good job of looking for the issues and explaining them.
We're happy to know our team was thorough in diagnosing the problem and clear in their explanations. We value your 5-star review and look forward to assisting with any future HVAC or plumbing needs. Thanks for choosing LBA Air Conditioning, Heating & Plumbing!