Mission Hills, KS Residential HVAC & Plumbing Services
LBA Services was started by people just like you who want and insist on high quality and reliable service. In Mission Hills, KS and throughout the Kansas City area, we treat each family and home as if it were our own. That includes rising to the challenge of being a Hero any time the need calls for extraordinary measures.
From routine maintenance to 24/7 emergency repairs, LBA Services has you covered for all your home plumbing, heating, and air conditioning needs. The same goes for new and replacement system installations. Read our reviews and find out why your neighbors consider us to be their nearby heating and air company and local plumber in Mission Hills, KS.
Recent Jobs and Reviews in Mission Hills, KS
Our Local Reviews by City
- Adrian, MO (2)
- Avondale, MO (1)
- Basehor, KS (21)
- Bates City, MO (1)
- Belton, MO (31)
- Blue Springs, MO (56)
- Bonner Springs, KS (30)
- Buckner, MO (1)
- Bucyrus, KS (6)
- Columbia, MO (1)
- De Soto, KS (22)
- Dearborn, MO (1)
- Edwardsville, KS (14)
- Eudora, KS (9)
- Fairway, KS (88)
- Freeman, MO (1)
- Gardner, KS (14)
- Gladstone, MO (63)
- Grain Valley, MO (32)
- Grandview, MO (69)
- Greenwood, MO (1)
- Houston Lake, MO (7)
- Independence, MO (175)
- Kansas City, KS (397)
- Kansas City, MO (2744)
- Kearney, MO (3)
- Lake Lotawana, MO (4)
- Lake Quivira, KS (18)
- Lake Waukomis, MO (4)
- Lansing, KS (2)
- Lawrence, KS (19)
- Leavenworth, KS (7)
- Leawood, KS (408)
- Lee's Summit, MO (150)
- Lenexa, KS (577)
- Liberty, MO (104)
- Lone Jack, MO (1)
- Louisburg, KS (5)
- Merriam, KS (20)
- Mission, KS (195)
- Mission Hills, KS (74)
- North Kansas City, MO (10)
- Northmoor, MO (1)
- Oak Grove, MO (9)
- Odessa, MO (1)
- Olathe, KS (591)
- Ottawa, KS (1)
- Overland Park, KS (1369)
- Parkville, MO (182)
- Peculiar, MO (1)
- Platte City, MO (12)
- Pleasant Hill, MO (1)
- Pleasant Valley, MO (3)
- Prairie Village, KS (506)
- Prairie Village New, KS (2)
- Raymore, MO (24)
- Raytown, MO (74)
- Riverside, MO (15)
- Roeland Park, KS (181)
- Shawnee, KS (990)
- Shawnee Mission, KS (1)
- Smithville, MO (1)
- Spring Hill, KS (11)
- Stilwell, KS (61)
- Sugar Creek, MO (7)
- Weatherby Lake, MO (26)
- Wellsville, KS (1)
- Westwood, KS (27)
- Westwood Hills, KS (17)
Job Locations and Reviews

Two return airs, new a/c and coil, new 90% furnace,two new return air drops,reinstall two humidifiers, rehook zoning up,new t-stat

Air Conditioning System Repair Service: I diagnosed a heavily soiled evaporator coil as the source of reduced cooling capacity. After a thorough cleaning, the system’s efficiency and comfort levels were restored.
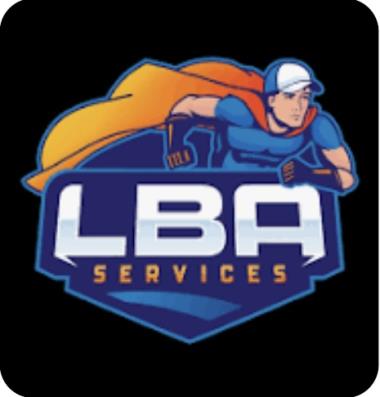
Sold main system AC/coil, second system furnace only, return ductwork/new drops & grilles on both. New thermostat, smart ac sensors, new annual membership.

Completed AC inspection for customer on both systems. There were issues found with both systems, field supervisor came to assist in service and provide advisement to customer. Customer has selected to replace damaged equipment as well as airflow modifications to correct inadequacies.

Water Heater Replacement: A homeowner sought a more efficient hot water solution, so I installed a high-performance tankless water heater, providing continuous hot water while optimizing energy usage.

New filter dryer, new return air ductwork and 20/20/1 filter grill, and changed a/c unit.
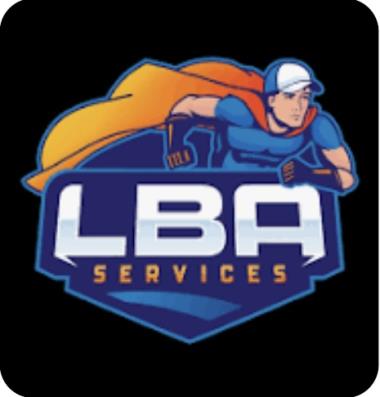
Sold 1 star duct package to fix flex ducting and sizing in attic and also replace filter drier $9260
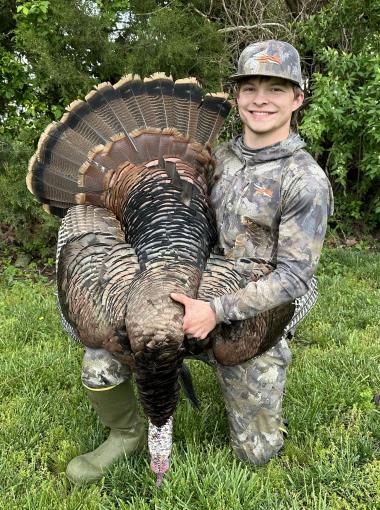
Went for an ac inspection today. Changed and cleaned filters. Static pressure failed for the Goodman system. Lennox air handler passed static pressure. Blower motor is over amping on York furnace. Evaporator coils are good for the Goodman, but the Lennox coil is rusted. Temp split for the Goodman was 19 and the Lennox was 17. Outside units are clean. Refrigerant levels passed on the Goodman. Fan motor and compressor amperage passed as well. Capacitor passed. Lennox refrigerant levels show a restriction. After performing a diagnostic test. I noticed the filter dryer is causing a restriction. The fan motor amperage is high and compressor amperage is passing. Hard start is still working correctly. Mimi split is cooling correctly. No leaks on the system. Has a clean coil. Thank you for choosing LBA services!

Sent email to mr. Troutman
JJ and Dre did a good job of explaining what was happening with my HVAC system and also went over all the possible options available to me.
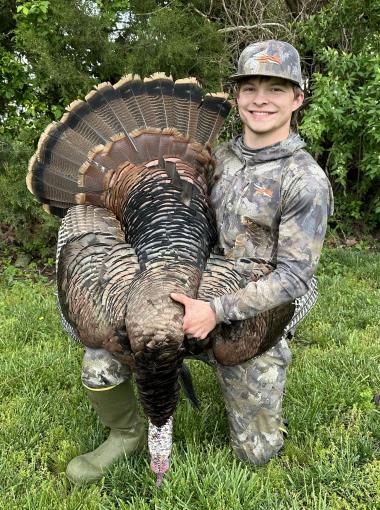
Furnace heat exchangers have failed. Furnace is disabled. Thank you for choosing LBA services!

Upon arrival the condensate pump was leaking from one of the PVC pipe connections. We took it apart and re-glued the pipe fittings and we no longer have any leaks. We did leave a dry bowl under the pump where it was leaking before. If she has any more trouble with it she will let us know. If you have any questions or concerns please feel free to call us! Your LBA Technician, Tyler Rickard P.S. No payment was due for todays visit. Have a great week!
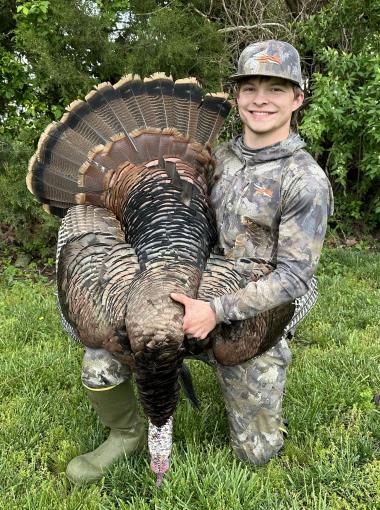
Furnace is running great

L

Installed new FR951V1005A21M4 Furnace and replaced the inducer motor on existing 2016 Lennox Furnace. Equipment Warranty 2 year labor warranty 10 year parts warranty Existing Furnace Part Warranty 1 year

W
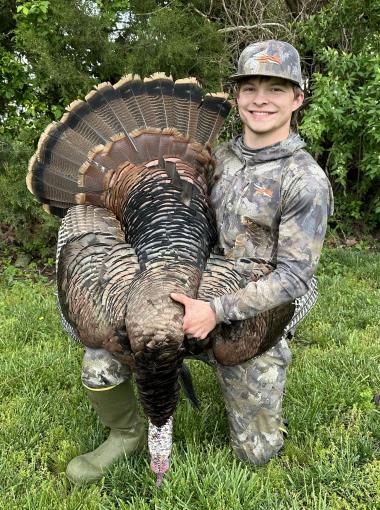
One furnace is leaking carbon monoxide. The other furnace passed on airflow, safety inspection, and all parts passed but the inducer motor is over amping. Thank you for choosing LBA services!

Hybrid Furnace Repair: A malfunction in a hybrid furnace’s electric heating module left a home without sufficient warmth. We repaired the module, ensuring efficient heating while minimizing energy consumption.

Inducer has been replaced on crawl space unit left it up and running

Ductwork Repair: A homeowner complained of inconsistent airflow in their central AC system. After testing the duct system, I found several disconnected and crushed ducts in the attic. I repaired the connections, reinforced them with sealant, and added support to prevent future collapse. The homeowner reported a noticeable improvement in cooling efficiency.

Replacing inducer tomorrow on crawl space unit and installed smart ac sensor on main unit

80% efficient w/ 2 stages of heating and variable speed fan 10 year parts warranty Bypass humidifier x2

2 failed hx

Upon arrival I began the furnace tune ups. This home has two 3 ton systems. Both furnaces are 2014 Lennox so they are both 10+ years old. I started with a static pressure test on the main floor unit. These systems are rated for .8 maximum static pressure and the main unit is testing at .8(right at the max). Next, I did a CO test on the main unit. I got hits of CO on my meter at 129ppm(parts per million). Per EPA rules & regulations we are required by law to shut the units down by shutting the gas valve off. I have done this on both units because the 2nd floor unit was also leaking carbon monoxide. I took pictures of the heat exchanger the best I could. The blower wheel on both units are very dirty. My Field Supervisor Jamie has arrived to help find some solutions for the homeowner. If you have any questions or concerns please feel free to call us. Your LBA Technician, Tyler Rickard P.S. No payment was due for todays visit, it was covered with your membership. Have a great holiday!

Re piped lavatory sink with new 1-1/4 plastic pee trap and new pop up assembly. Tested for leaks everything looks good.

Sold
We so appreciate the thorough explanation and discussion of options to get our system repaired
It was a pleasure serving you and your family. Thank you for sharing your kind words with us. It means the world to us and to our entire team!
Very knowledgeable and helpful!
We thank you for sharing your positive experience. It made our day.
Scott asked me what I was looking for and after I told him he put together a good, better best presentation of three different systems. He explained what each was about and asked when I might be making a decision. I told him I would get three bids and, then get back in touch with him. He didn’t ask when he could call me and I said it might be best to wait a couple of weeks.
Johann was very polite and concerned about my needs. He showed me the problems with my appliance and suggested needed repairs. Since I was am considering a new system, I told him I would wait. You have a very good employee who represents your company very well.
Chase was very knowledgeable and thoroughly explained everything.
I have never been more disappointed with the service I received. I think it is ridiculous that I was without hot water for two weeks and I have a new $6500 water heater. I asked repeatedly to have someone in management to call me and didn’t hear from anyone. I have been a loyal customer for decades and was treated like I didn’t matter.
Very professional who good service
Polite and thorough
Very polite and accommodating
Problem was corrected quickly! Nick was friendly, knowledgeable and very professional.
Patrick arrived on time and explained the process of inspection of our two units. He spent considerable time and care and communicated what we need. Patrick was polite sincere and competent.
Great service!
Thank you for the 5 Star Review!
Great service!
Extremely knowledgeable ,honest , helpful , thorough , and professional No complaints at all and extremely pleased with his work . Personable, and hard working to complete the job .
I was impressed at how friendly and helpful the technician was. He explained everything to me in regard to what he did and what needed to be done. Because of him I am going to sign up in January for the yearly package.
LBA came to the rescue on furnace and hot water heater problems today! Excellent service from the two very nice gentlemen service techs.
Very professional and courteous.
No solution. Trip call charge
Excellent worker installed new unit without help. Worked hard for hours without a break. Thanks
Great service. Came back after new unit not working and helped with wifi thermostats too. Thanks.
Nick is very professional and communicates very well. Wore his mask.
The problem was fixed at reasonable cost!
Eli was a very respectful service professional and answered all my questions. He was very considerate of my home and did the work in a timely fashion. I would be happy to recommend him to anyone.