Pleasant Valley, MO Residential HVAC & Plumbing Services
We all want the same things. The love of family and friends. Food on our table. Time to spend on things we enjoy. And a comfortable home. We can't help you with the first three - but we've got you covered on number four. The team here at LBA Services has decades of combined experience working on heating, air conditioning, and plumbing, and we're ready to bring that experience to your home today. Whether you're looking for AC repair, a furnace replacement, or just want to redo your kitchen plumbing, our experts have you covered. At LBA, we consider perfect to be our minimum standard - meaning that when you call on us, we'll provide solutions that are perfect for your needs, your home, and your family. Trust us with your HVAC & plumbing services and you'll never be disappointed - just call our team at 913-268-6822 today!
AC Repair In Pleasant Valley, MO
We pride ourselves on delivering top-notch AC repair services backed by years of industry experience. Our team of dedicated professionals is committed to ensuring your air conditioning system operates at peak efficiency, providing comfort and reliability throughout the warmer months. We understand the importance of a well-functioning AC unit, which is why we offer comprehensive diagnostics and repair solutions tailored to perfectly address the unique needs of your system. Trust LBA Services to handle your air conditioning repairs with the utmost care and expertise, ensuring your home remains a cool refuge even during the hottest days.
Furnace Replacement In Pleasant Valley, MO
Our commitment to excellence shines through our furnace replacement services. With decades of experience, our skilled technicians are dedicated to providing seamless and efficient heating installations, ensuring your home stays warm and cozy during the cold seasons. We understand that replacing a furnace is a significant investment, which is why we focus on delivering tailored solutions that meet your specific heating needs and budget. Rely on LBA Services for a smooth and professional furnace replacement experience, leveraging our expertise to enhance your home's comfort and energy efficiency with minimal disruption.
Duct Cleaning In Pleasant Valley, MO
Clean ducts are an important part of maintaining pristine indoor air quality in your home. Our experienced team dives deep to remove dust, allergens, and debris from your ductwork, improving the air quality of your home and enhancing the efficiency of your HVAC system. We are dedicated to providing a clean and healthy environment for your family, using advanced techniques and equipment to ensure comprehensive cleaning. Choose LBA Services for your duct cleaning needs and let us be your trusted partner in having clean, healthy indoor air.
Drain Cleaning In Pleasant Valley, MO
We offer specialized drain cleaning services designed to resolve any clogging issue swiftly and effectively. Our team, armed with extensive experience, is dedicated to ensuring that your drainage system is free of obstructions and functioning optimally. We use state-of-the-art technology to diagnose and clear blockages, preventing potential backups and water damage. We are committed to delivering perfect service, exceeding expectations with every job. We'll take care of your drains so you can take care of what matters.
HVAC & Plumbing Service FAQs
Replacing a central heat and air system in the Pleasant Valley, MO area typically ranges from $5,000 to $10,000. Several factors influence this cost, including:
- The dimensions of your home.
- The model of HVAC system you choose.
- The expenses involved in removing your old unit and installing the new one.
Investing in a new central heat and air system can be a significant upfront expense, but it offers long-term savings on energy bills and enhances your property's value. For more details on upgrading your central heat and air system, don't hesitate to contact us today.
In Pleasant Valley, MO, there are several signs that might indicate a blockage in your main drain or sewer line:
- The presence of a sewer smell or backup in your home.
- Gurgling sounds coming from your drains or toilets.
- Water backing up or flooding in your home.
A clogged main drain or sewer line requires prompt attention to prevent damage to your property. Furthermore, persistent sewer odors can also pose health risks. If you suspect a blockage, contact us immediately to have your main drain or sewer line cleared.
Minor HVAC repairs, including replacing fuses, breakers, or thermostats, typically cost between $150 and $290. For more extensive repairs, such as fixing a refrigerant leak or an evaporator coil, prices can range from $200 to $1,500. Generally, AC repair costs vary from $125 to $459, whereas furnace repairs usually fall between $125 and $355. Bear in mind, these are all estimates, and the final pricing will depend on exactly what is happening at your home. You can be assured we'll provide an honest, upfront quote before we do your work.
Is your HVAC system malfunctioning? Reach out to LBA Services today for prompt and professional assistance.
Recent Jobs and Reviews in Pleasant Valley, MO
Customers say: The provided content describes the overall sentiment of the reviews as positive. The reviews mention specific individuals who were helpful, professional, informative, trustworthy, patient, thorough, friendly, knowledgeable, and helpful. There are also mentions of quick and efficient service, confidence in choices, and satisfaction with the work performed. However, there are also negative reviews that mention issues with pricing, communication, and the experience with technicians. Overall, the sentiment is positive, with more positive reviews than negative ones.
Our Local Reviews by City
- Adrian, MO (2)
- Avondale, MO (1)
- Basehor, KS (21)
- Bates City, MO (1)
- Belton, MO (31)
- Blue Springs, MO (56)
- Bonner Springs, KS (30)
- Buckner, MO (1)
- Bucyrus, KS (6)
- Columbia, MO (1)
- De Soto, KS (22)
- Dearborn, MO (1)
- Edwardsville, KS (14)
- Eudora, KS (9)
- Fairway, KS (88)
- Freeman, MO (1)
- Gardner, KS (14)
- Gladstone, MO (63)
- Grain Valley, MO (32)
- Grandview, MO (69)
- Greenwood, MO (1)
- Houston Lake, MO (7)
- Independence, MO (175)
- Kansas City, KS (397)
- Kansas City, MO (2744)
- Kearney, MO (3)
- Lake Lotawana, MO (4)
- Lake Quivira, KS (18)
- Lake Waukomis, MO (4)
- Lansing, KS (2)
- Lawrence, KS (19)
- Leavenworth, KS (7)
- Leawood, KS (408)
- Lee's Summit, MO (150)
- Lenexa, KS (577)
- Liberty, MO (104)
- Lone Jack, MO (1)
- Louisburg, KS (5)
- Merriam, KS (20)
- Mission, KS (195)
- Mission Hills, KS (74)
- North Kansas City, MO (10)
- Northmoor, MO (1)
- Oak Grove, MO (9)
- Odessa, MO (1)
- Olathe, KS (591)
- Ottawa, KS (1)
- Overland Park, KS (1369)
- Parkville, MO (182)
- Peculiar, MO (1)
- Platte City, MO (12)
- Pleasant Hill, MO (1)
- Pleasant Valley, MO (3)
- Prairie Village, KS (506)
- Prairie Village New, KS (2)
- Raymore, MO (24)
- Raytown, MO (74)
- Riverside, MO (15)
- Roeland Park, KS (181)
- Shawnee, KS (990)
- Shawnee Mission, KS (1)
- Smithville, MO (1)
- Spring Hill, KS (11)
- Stilwell, KS (61)
- Sugar Creek, MO (7)
- Weatherby Lake, MO (26)
- Wellsville, KS (1)
- Westwood, KS (27)
- Westwood Hills, KS (17)
Job Locations and Reviews
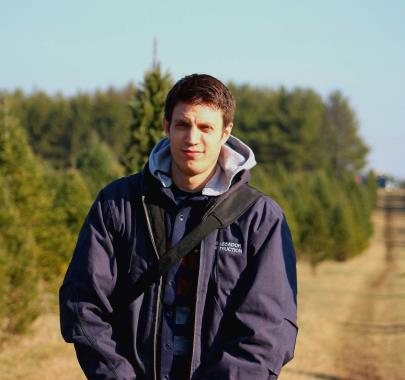
Doing routine maintenance for a furnace and AC. After checking everything all components. Are operating under manufacture specifications. I cleared out the drainage, hose and suction line and cleaned off the heat sensor. Static pressure is still high and at some point should be addressed. In the meantime, I did lower the fan speed by one to ensure that we are putting too much static pressure on the system, even though we are still far over its max.

Duplicate job

Found loose and leaking union. Tightened the union and performed soap and bubble gas leak search. System is sealed.

Happy call

Arrived to customer for a furnace tuneup in during the process of the inspection receive the high, called on static pressure along with discovering a dirty filter. All other components met within factory specs.

Na

Went for a check in. Talked to customer about our membership. Did the transition. Will have membership for 1 year free. Once membership expires, renewal will have to be made. Installed smart ac sensors. Customer was able to login into account. Checked static pressure static was in factory specifications. System are both running before leaving. Thank you for choosing LBA services.
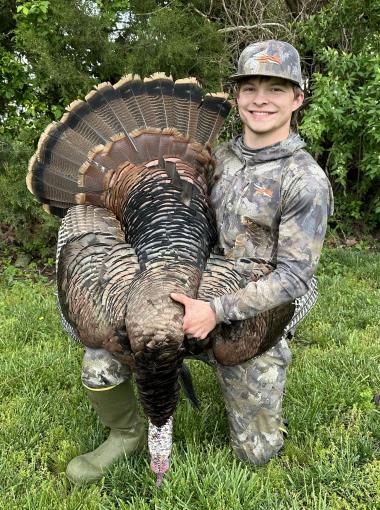
Went for a maintenance call today. Started at the furnace. Did a static pressure test, it was high. After adjusting the blower speed, it passed. Did a cubic feet per meter count, it passed. Temp split between the supply and return duct passed. Blower motor amperage passed. After analyzing the blower wheel, I noticed it was dirty. Changed filter due to being dirty. Outside unit got washed. The amperage for the compressor and the fan motor passed. The capacitor passed as well. Thank you for choosing LBA Services!

Customer declined

Gary and Cindy said they would have fixed the air flow when the equipment was installed a year and a half ago, but we hadn’t rolled out the airflow program yet. Got approval to offer retroactive airflow pricing, primarily for the 2 and 1 star duct packages. Cindy is diabetic and was hungry and overwhelmed. Following up on Monday so they have the opportunity to settle on their preferred solution.

Arrived for AC maintenance today. Started at furnace and checked static pressure, temperature splits, drains, filter, blower wheel, blower motor. Static is failing at this time, a field supervisor will be out to discuss. Put in our high velocity filter to ease some of the pressure. Wheel is starting to collect dust and could be cleaned. At the ac unit refrigerant was good. Capacitor is reading within specs. Running amps are good. I rinsed coil clean. System is running upon leaving. Thanks for choosing LBA.

DATE - 6, august 2024 Performed whole home inspection Vitals: -Total Dissolved Solids: 246 cold, 329 hot -Water Pressure Static: 50 -Water Pressure Faucet Open: 50 -Water Temp Setting: 120 -Water Temp Output: -Water Hardness: 9 -Water Quality: chlorine 2, ph 10 plus -Water Heater: 50 gallon gas, 2012 -Water Lines: copper -Drain Lines: abs Wear and Tear: thermal expansion tank, flex p trap tubing After reviewing the entire house I went over everything with joy to ensure they understood everything going on in the house and what could be done to address it. Solutions: install new thermal expansion tank, replace under sink p trap Services done today: performed whole home inspection, gave quotes for repairs Thank you for choosing LBA Services Your technician, mick ____

Joy mentioned that the upstairs, particularly the room above the garage, has never really kept up when it is hot out. Her system is pulling in only half of the required air, causing irreversible damage to both her indoor and outdoor systems. The airflow system is broken. The air pressure at the system is so high that it causing the unit to “whistle”. Pulled registers to help relieve some back pressure as a temporary measure and increased the temperature at the thermostat so the system wouldn’t run as often. Joy said she needs to go over a few things. Joy wants to select and schedule her preferred option at that time.

Arrived to do a performance maintenance. Started inspection inside and measured a temperature split between return and supply air. Measured power consumption of the blower motor and checked system for cleanliness. Found bacterial growth present on the condensation pan for the evaporator coil and the blower wheel is coated in dust debris. Performed a static pressure test and found that the system is operating within manufacturers specifications. Went outside and verified system refrigerant charge. Verified operation of all mechanical and electronic components of the condenser. Rinsed coil free of debris. Spoke with homeowner about the system. Air conditioning system is operational at this time.

Performed full inspection, presented options for replacing a few issues. Performed water line check and adjusted to different location per request

The airflow packages and pricing vary per job. They also wouldn’t make sense to customers if a customer doesn’t know what’s going on. Only way for customer to understand wahatsngoinf on Andy the pricing included would be if we go over that stuff with them. That said we don’t just email prices because that would be in vain.
Looking at the pictures more closely it is not even the date of when they were here. I had a small locally owned independent company come out to give me their opinion. They found NO cracks and stated the duct work is totally sufficient for my home. I feel I was perhaps scammed. Independent contactor restarted furnace and ran carbon monoxide test and detected absolutely no carbon monoxide. I hesitate but am inclined to inform authorities of possible deceptive business practice.

Showed customer failed airflow readings and why we were getting those readings. We talked about options and what could be done and what was most cost efficient. Customer would like a second set of eyes on heat exchanager. I left customer my number and set up a follow up call for next week.

Arrived for AC MAINTENANCE. Ran static pressure test and found it to be operating above designer max static. We opened up vents in the home and installed a clean filter. Static pressure dropped some but is still failing. With the inspection camera we found a crack in the heat exchanger. Showed home owner the crack and signed a red tag. Called out supervisor to finish diagnosis on static pressure. Ran amp draw on outdoor unit and everything passed. Good charge on refrigerant. Performed coil cleaning. AC is operating well at this time, furnace is disabled due to unsafe operating conditions.

Ductless System Installation: Responding to a client's need for targeted cooling, we suggested and installed a ductless air conditioning system. This addressed their desire for zone-specific climate control, ensuring customized comfort throughout the home. Routine maintenance checks were recommended to uphold the system's efficiency.
Technician showed up an hour and 15 min late, shrugged shoulders saying he had a long drive across town. Said it would take him an hour for the check-up on the AC, but he'd try to hurry. He was done in less than 15 minutes so I question how thorough he was. Did not review any of his findings. Did not ask if I had any questions, but asked if I wanted to renew my yearly check-up ... and I said definitely not. Also, was not contacted about my yearly AC check-up until August ... at the tail end of the summer. If I had problems with my AC, they should have been doing check-ups early in the season. In the past, the technicians have been wonderful, but this guy was awful.
It's very nice to have someone sit down and explain things to me, he didn't rush and I felt like he cared about the service he was providing, he's great